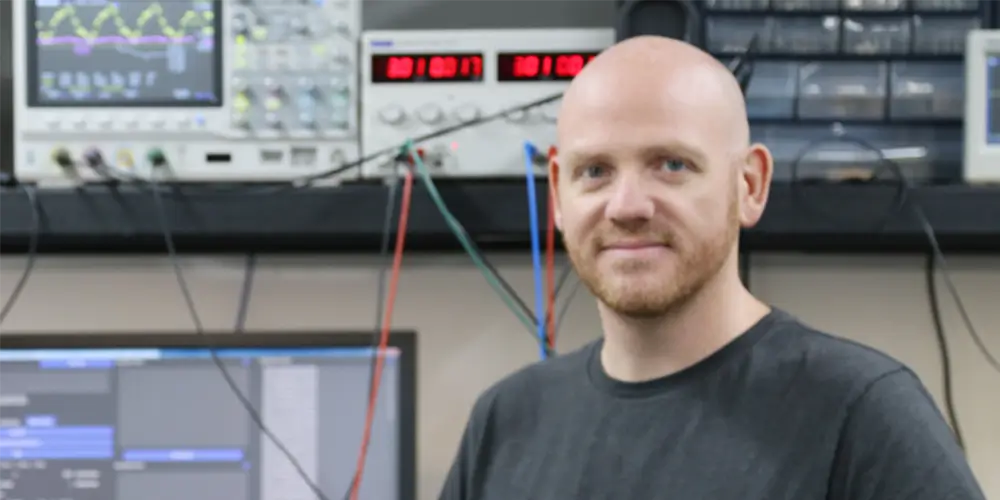
We spoke to Senior Product Developer, Aaron Russell about how his passion for improving people’s lives led him into the field of electronics. We also discuss common misconceptions about the field and what to look for when choosing a design and development partner for your product’s electronics.
IDE: What are some of the biggest misconceptions about electronics in product design and development?
AR: Electronics is mysterious to most people. People often think that it’s some sort of magic; it does its thing and just works somehow, sometimes similar to how people treat computers. Since electrical signals cannot normally be seen, a lot of what is working in the background just isn’t apparent to people or easily understood. This can sometimes lead people into the trap of thinking electronics is the “easy” part of a product’s design and development. In reality, there’s a lot of work that goes into making sure a product’s electronics works reliably and can be produced at scale.
IDE Group (IDE): How did you get to where you are today, working for IDE?
Aaron Russell (AR): I’ve always been interested in technology and how it has helped us do things better, quicker, and safer; in fact it’s why I studied electrical engineering. I’m passionate about creating tools that can minimise frustration and give people an easier life. One of the reasons why doing this for IDE is cool is because that’s what we do here every day, while improving people’s lives.
IDE: Such as?
AR: For example, tolerancing issues exist in electronics design, similar to other areas of a product’s design. For mechanical parts, a tolerancing analysis might be broken down into a few critical parts and a handful of subset components. However a similar analysis for electronic parts might produce hundreds of parts with enormous amounts of subset components. If you’re making a million devices with electronic parts, every single one of them needs to work. So there’s a huge amount of analysis that goes into that. It’s not magic.
IDE: What about for medical devices?
AR: For medical devices, electronics need to meet all of the medical electrical standards and devices need to work perfectly, regardless of whether one or a million or more are made.
IDE: With that in mind, what should people look for when searching for a partner to design and develop their medical device’s electronics?
AR: Look for a company that has a good understanding of risk management, the electrical standards and their application. I’d also suggest looking for someone who has a clear track record of taking products through regulatory approvals, such as CE mark or listing with the TGA.
A good example of why this matters recently played out in my life. I ordered a product from a team on Kickstarter, which is actually a relatively simple device. The team had manufactured the devices in the past but had since moved to a different communications technology, and to different countries. All of a sudden the team found their broadened market brought with it far greater regulatory requirements. The product was supposed to be shipped in May 2017. Now it’s looking like June 2018. The point is that if the team knew this in advance, and had experience with this industry, they could’ve planned for it, but most importantly, they could’ve designed for it too. If you fail to design for things like this, you’re going to have to redesign somewhere down the track to meet a significant requirement that you never knew existed.
When (not if) the unexpected happens, traceability is also crucial. No matter who you choose to partner with, it’s important your product’s development history is captured through design controls and documentation. This is part of being a good engineer, but it’s also part of meeting ISO 13485 and giving your product the best chance at success.